Welcome to Part II. about mass timber architecture.
My team’s experience with mid-scale mass timber
So far, we’ve designed one small multi-family build and two office buildings of which the first one was built in 2021. It was a 1200 m2 office with the structure built in 24 workdays, with a team of 4 carpenters, a crane and me as the commander!
Through these projects, we realized that mass timber is an extremely underrated technology. In fact, it is one of the few true construction innovations I advocate for.
In PART I, I introduced mass timber and discussed its use in homes. Now, let’s explore the advantages it offers for larger developments.
Unique advantages of mass timber in mid-rise developments
You get up to 14% more useable area with mass timber!
The first multi-family project we completed in 2014 was a small four-apartment building with only 260 m² (2800 sf) of total usable area. Thanks to the slimness of the mass timber structure, we gained an additional 37 m² (400 sf), enough for a small studio. This resulted in a 14% increase in usable space on a compact urban plot.
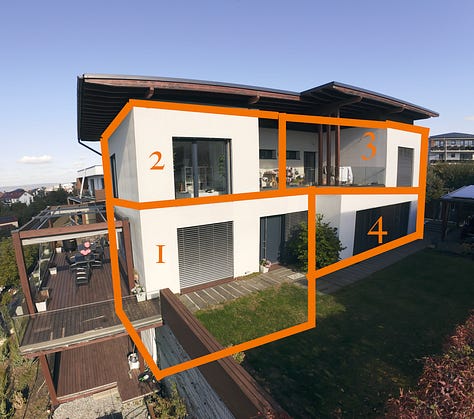
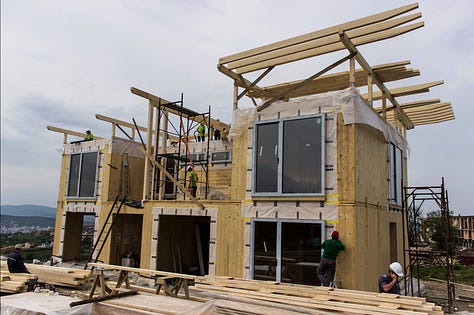
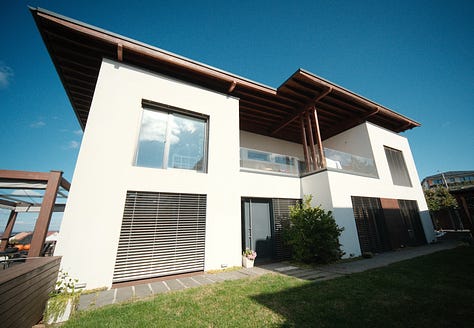
In the two office buildings, we gained 101 m² (1100 sf) and 31 m² (400 sf) respectively, averaging an 8% increase in usable area.
Earthquake-proof floor and wall panel system without bulky columns
The diaphragm structure allows for the construction of buildings up to six stories using slim structural load-bearing and shear walls, only 10-16 cm (4-6 inches) thick. These walls provide 25 times more insulation than concrete and are earthquake-proof, eliminating the need for bulky columns in residential buildings.
Building speed - 1 floor per week
With good planning, a new floor, up to 500 m2 (5400 sf) can be built, so a 6 storey building’s structure can be finished in 7 weeks, including foundation prep and logistics. Not to mention you can build it in any climate, in any season with no constraints.
Post and beam mass timber
Another approach is the post-and-beam mass timber system, which offers greater flexibility in floor plan design. For example, the AscentMKE project in Milwaukee, helmed by Tim Gokhman and currently the tallest mass timber building in the world, utilizes this method.
We will analyse another post-and-beam solution in a case study in Part III.
Reduced interior finish lead time
As mentioned in Part I, mass timber surfaces can often be left exposed,* significantly reducing the time required for interior finishes. For example, in our most recent home project, 350 m² (3700 sf) of exposed surfaces were sanded and spray-painted by two workers in just four days.
*Provided it complies with local fire safety regulations.
Reduced weight on the foundation - Dalston Lane, London, UK by Waugh Thistleton
In some scenarios, the number of apartments you can build is limited by the weight of the foundation can bear. For example, on Dalston Lane, London, the site was undercut by a subway line that imposed strict limits on the building’s maximum weight. Choosing mass timber as a structural solution yielded an extra number of 40(!!!) apartments for the developers.
Better energy efficiency
As I’ve mentioned numerous times on Twitter and in Part I, mass timber inherently insulates 25 times better than concrete walls and is airtight when thicknesses exceed 4 inches. This eliminates the need for vapor barriers and allows for reduced insulation in colder climates while maintaining the same R-value for the wall assembly.
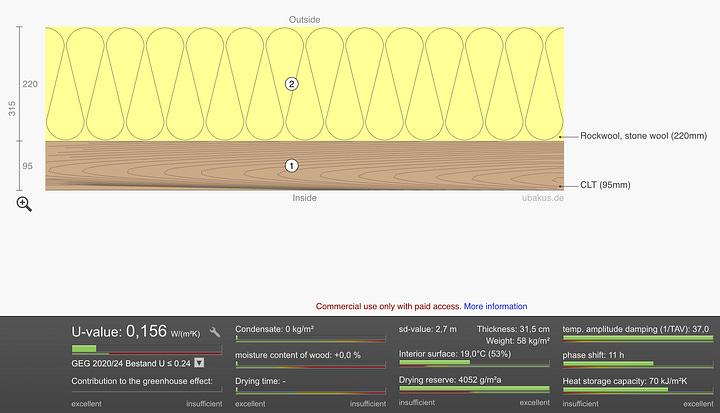
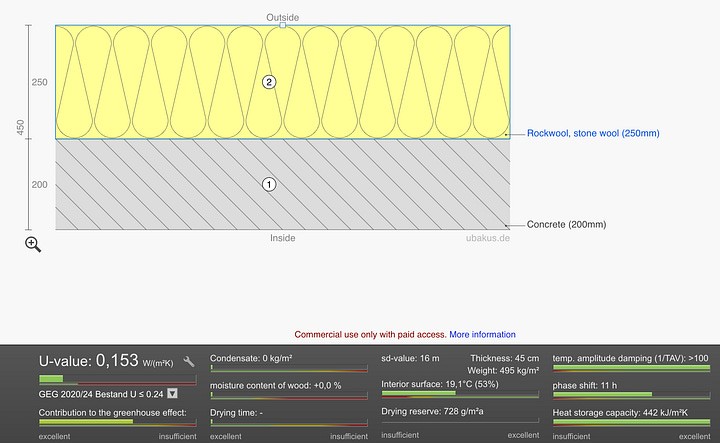
If you’re interested in exploring mass timber further, you can book an exclusive 90-minute one-on-one consultation with me! Worth it if you have a RE project you want to take to the next level!
In Western Europe, numerous mass timber apartment buildings are being constructed in various shapes and forms, often on constrained urban sites.
Mass timber apartment buildings
For example, a six-story, single-stair mass timber project done in Paris, features 10 sunlit apartments on a tight urban infill site, all with the natural ambiance of wood.:
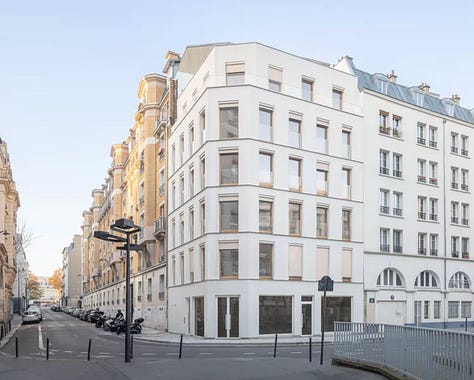


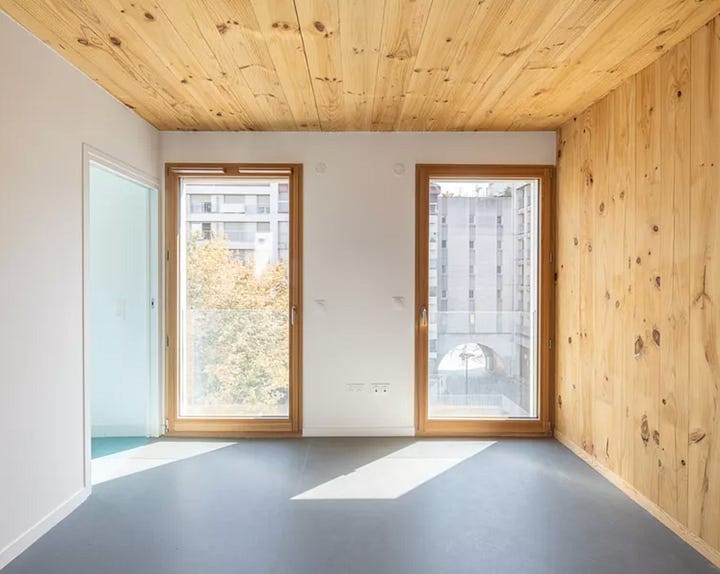
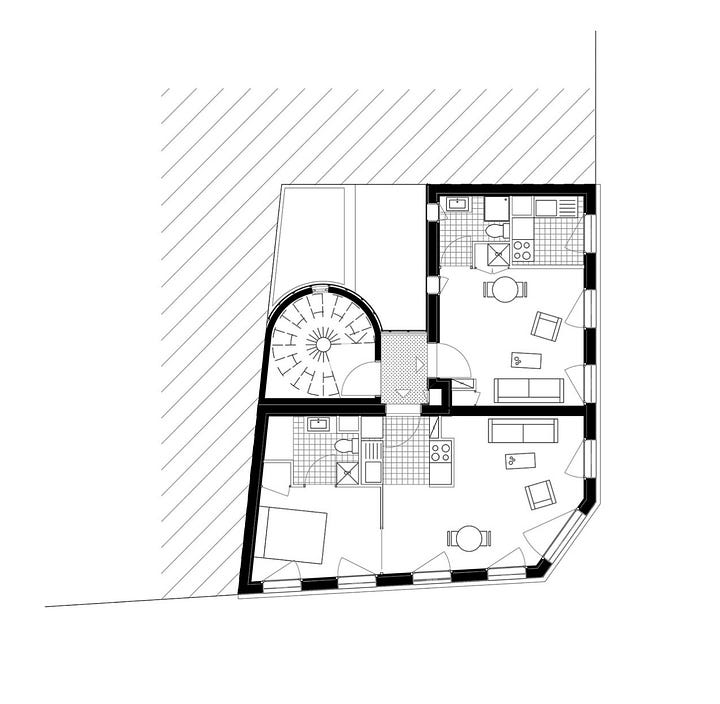
Are you smelling the timber scent yet?
And here’s a 2 floor mass timber extension over a Victorian building by Waugh Thistleton, again taking advantage of the high-performance lightweight structure. Old and new blend so well together, you can’t even notice!
Scaling up mass timber
We can build mass timber factories anywhere using local soft timber species that can yield 1x4s. For instance, the entire structure of our 1050 m² project was transported in just nine standard European trucks, demonstrating efficient logistics.
Once factories are within 600 km of any location, transport costs will decrease and it will get even more competitive. Rising labor costs make millimeter precision mass timber an even more economic and durable solution.
That concludes Part II. Stay tuned for Part III, where we will provide a more detailed analysis of our case study projects.